车企数字化丨研究报告
核心摘要:
发展背景:
生产数字化理解:生产数字化是利用数字化技术,解决现有生产制造方式不能满足客户需求的核心问题,同时将生产流程、工艺中的不确定性降到最低。
转型驱动力:国家政策和地方细则双轮驱动;消费者个性化需求对于生产提出更高要求;数字化转型保证企业竞争力;依赖经验的生产决策急需数据能力全面优化。
发展现状:
转型目标:利用数字工厂将传统汽车生产制造方式转变为柔性化生产方式,以便快速的响应消费者个性化需求,以及降低为了满足消费者需求而产生的一切不确定性和风险。
困境与挑战:顶层架构缺失导致的内生动力不足;由于缺乏数字化认知导致的转型失灵;看重投资回报率,难以接受投资回报不明确下的巨额支出;生产端附加价值较低,难以获得高层重视。
转型建议:自上而下:在集团层面设立数字化部门,自上而下贯彻数字化路线;纲举目张:抓住自身企业数字化的关键所在,以点带面、小步快跑;生产效率提升并非一蹴而就,配置临时人员可促进产能提升。
发展趋势:
数据分析:数据分析工具和人才需求不断增长,既了解汽车制造又能够熟练使用数据分析工具的人才将在行业中获得巨大的竞争力。
5G工厂:5G将成为数字工厂的重要通讯手段之一,其大带宽、高可靠性和低延时等性能在汽车制造中的适合用性不断提升。
协作机器人:机器人在制造业中的持续优化及演进,人机共融的生产方式将重塑人们对制造业的刻板印象。
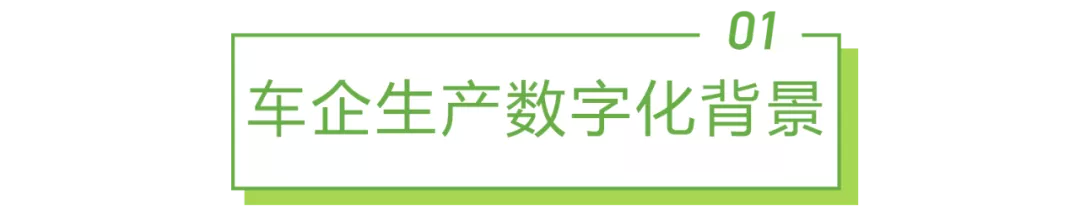
何为生产数字化?
生产数字化是应用数字化技术,以满足客户定制化需求为本,以应对车企生产不确定性为核心的生产变革手段
目前,中国车企在制造端面临的核心问题是现有的制造方案不能满足客户个性化、定制化的购车需求,大批量制造的同质化产品已无法得到客户的青睐,因此车企为提升自身竞争力开始尝试小批量定制化产品。至此,客户对于质量、配置、服务和交付时间要求的不确定性倒逼车企必须对整个生产流程做出改变,而生产数字化便是车企生产流程变革的重要手段。生产数字化虽然可帮助车企优化生产排期、工艺流程等达成减本增效,但自动化设备的使用、制造经验的提升和精益制造的理念已将生产效率成倍提升,边际效应愈加明显。因此,艾瑞认为,车企生产数字化的核心在于利用数据能力应对消费者需求转变所带来的潜在风险,将生产流程、工艺中的不确定性降到最低,其为车企提供的长期隐形价值将远远超出想象。
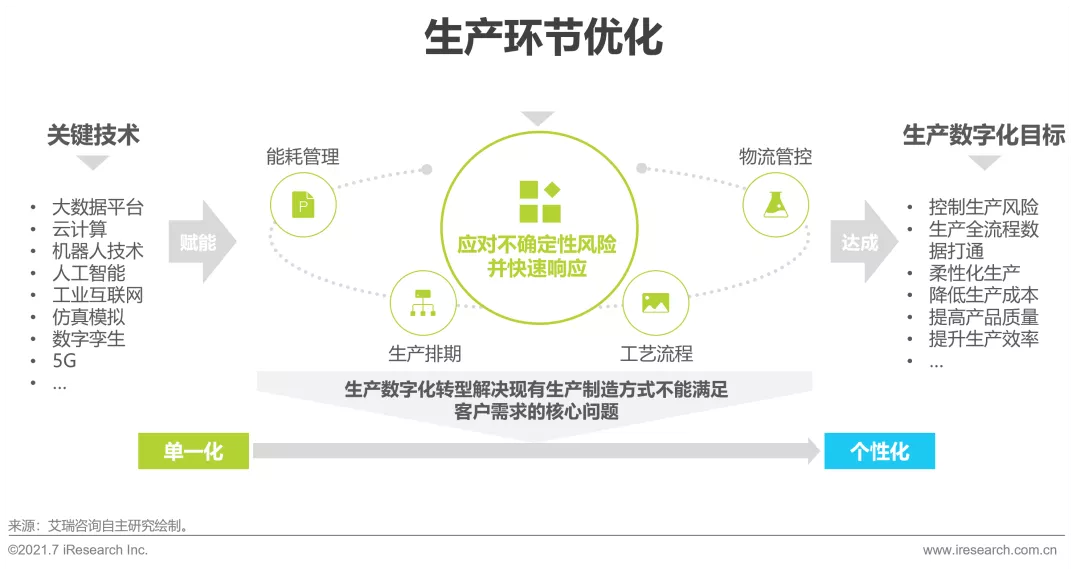
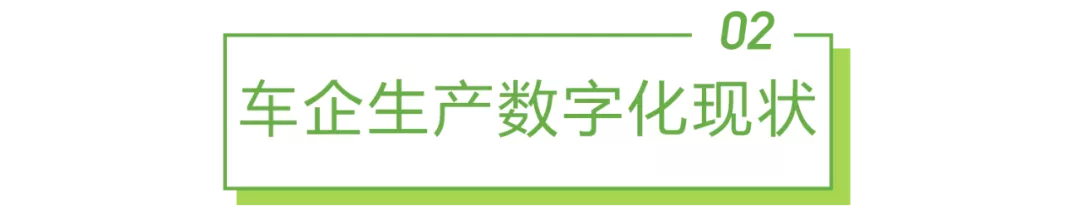
汽车制造四大工艺简述
冲压、焊接、涂装、总装
冲压:由于工作环境较为恶劣,通常为简单、批量化的工作,因此自动化率可达90%以上。但其数字化程度相对较低,因为其虽然要求在达到一定精度内的大批量生产,但可通过库存来解决多数问题。焊装:焊装是汽车质量分界点,工艺相对复杂,环境恶劣,部分操作要求带有计算机视觉的设备进行自动化激光点焊,自动化率可达80%~90%,但由于分拼线和表面调整线操作较为复杂,仍需人工操作。涂装:工艺相对简单,由机器人按照既定轨迹喷涂即可,自动化率可达80%以上。但其过程少有复杂的数字化系统支持,因此数字化程度相对较低。总装:由于零部件种类较多且不规则,使用机器人成本较高,因此较为依赖人工装配,自动化率在20%~30%左右,数字化特征较多体现在工时优化和质量检测方面。

工业大数据如何改善生产方式?
数据透明化、敏捷化成为车企生产方式变革的根本所在
工业数据为车企生产环节转型的基础,而数据的透明化,决策的敏捷化是生产数字化转型的根本。通过在库存、制造、物流、质检等各个生产环节产生的数据进行有效连接,分析及使用,改变原有粗放的生产方式。用数据的透明及快速传输能力打造数字工厂,解决车企生产环节长久以来的遗留问题或未被发现的问题,从而精准管控生产效率,预防潜在风险便是工业大数据赋予车企生产环节的意义。
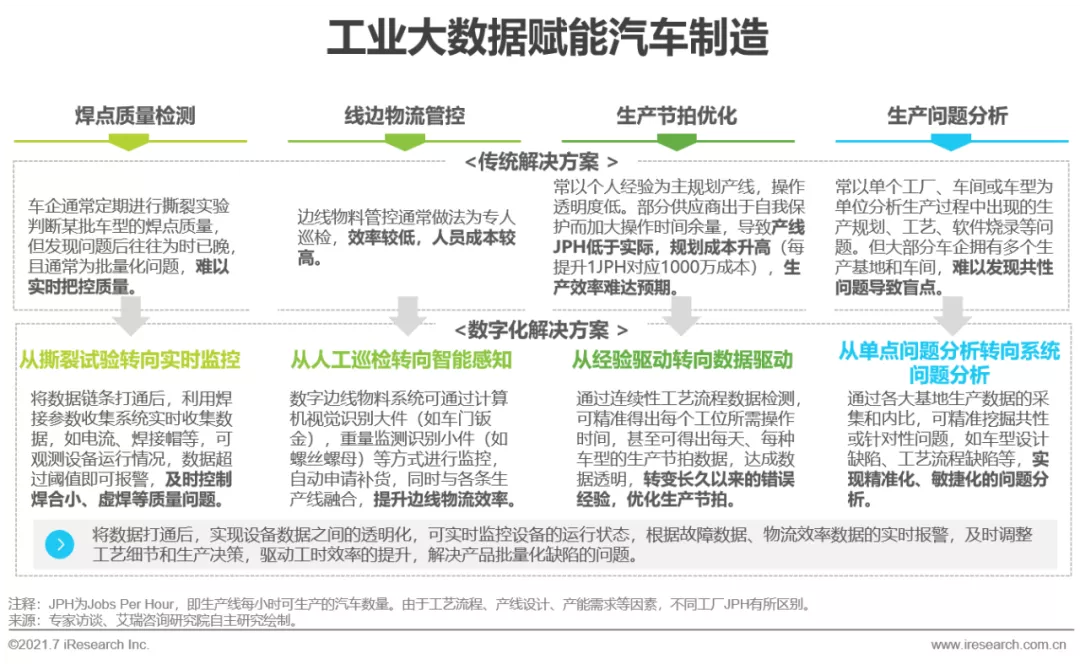
工业软件如何赋能生产控制?
处于执行层的MES赋能生产制造环节的数字决策
生产执行系统(MES)是车企生产环节重要的数字化工具,MES借助底层信息,根据上传的计划数据和生产实时数据做出反应、计算和展示。MES上接车间管理层下接设备,横向覆盖冲、焊、涂、总四大车间,可在生产、物流、人员、工艺、过程等维度做出快速响应,提高信息传递效率和精准度,有效降低由于不确定性因素导致的停工、错料等情况。
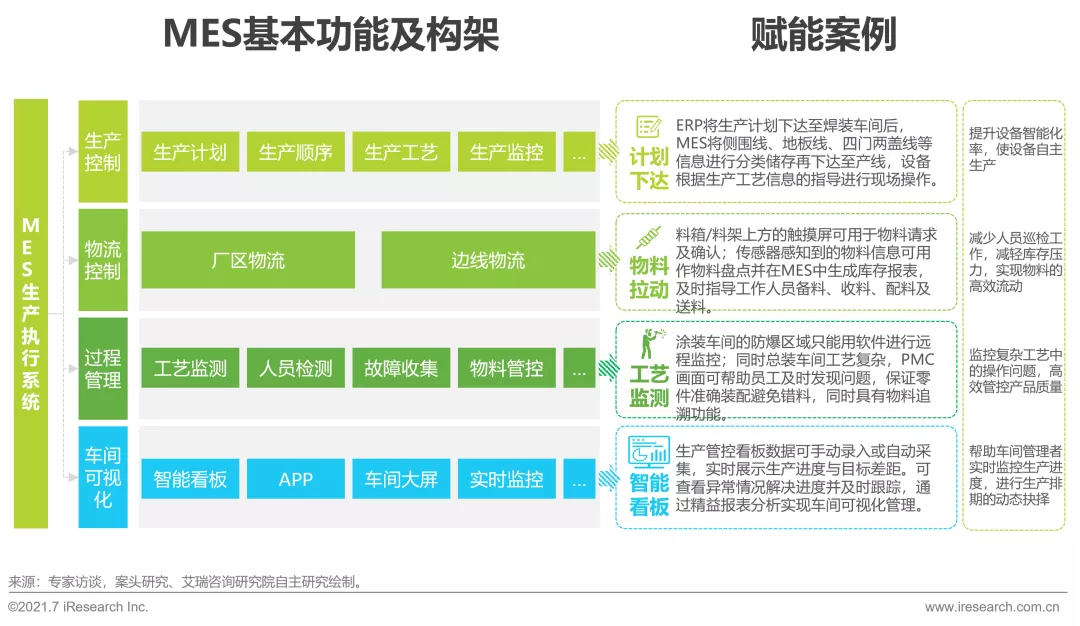
工业机器人如何提升制造水平?
利用机器人流程自动化和数据能力打造数字智能工厂
供应商帮助企业搭建自动化生产线的周期一般为6到18个月,取决于产线长度和制造工艺复杂程度等因素。在四大车间当中,出于焊装对质量、精度要求较高,涂装喷房中环境高温高湿且涂料异味较重,因此焊接和涂装环节机器人用量最大,从几十到几百台不等,取决于产线生产节拍。冲压环节因操作流程简单,机器人仅作为抓取、装卸使用,因此少量机器人便可满足需求。而总装环节本身自动化程度较低,除玻璃打胶、密封条粘贴等,其他操作机器人难以执行,因此部分企业用量在8~10台不等。总体而言,每个机器人的使用约代替5个人工,可将JPH从30提升至50以上,将OEE从70%~80%提升至90%以上,极大程度上提高生产效率及制造水平。然而机器人在自动化时代就被各大车企广泛应用,因此机器人在数字化时代的价值不仅仅是机器替代人工,而是通过挖掘机器人采集到的数据进行进一步分析赋能整个生产环节,利用机器和数据价值的叠加打造数字工厂,为智能制造和工业4.0打下基础。
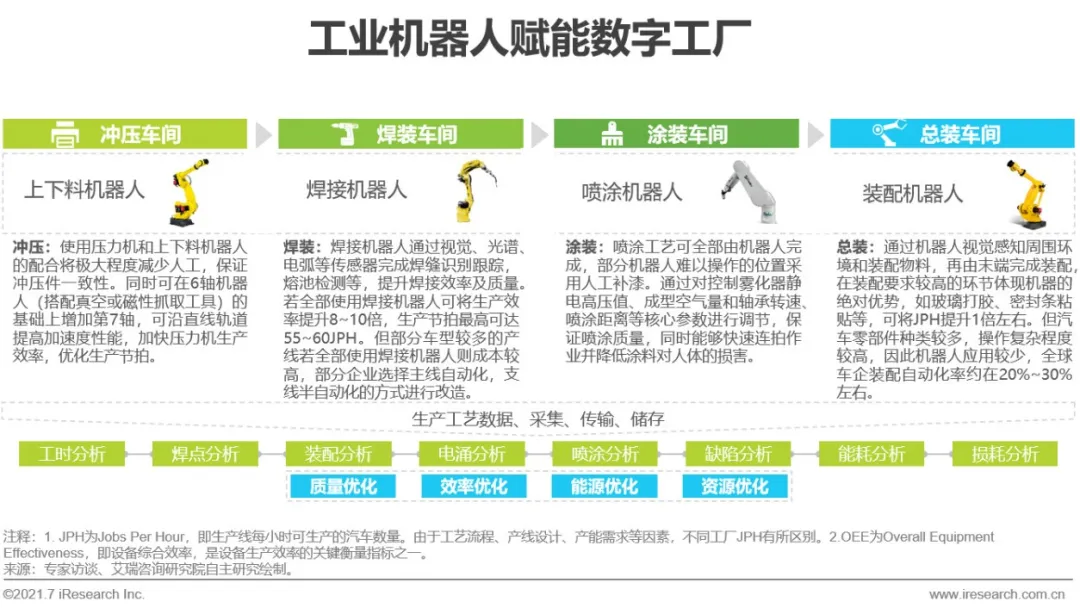
数字孪生如何进行模拟仿真?
利用数据透明化降本增效,减少生产环节不确定性因素
在利用数字孪生进行生产仿真时,规划人员利用无人机等现场勘测设备进行绘制产线的基本信息,同时利用工厂已有的历史信息作为参考设置变量和参数建立模拟工厂,其输出的结果可作为评价工厂具体指标的重要参考。例如,通过制造流程孪生体观测生产节拍、机器人工作状态和生产工艺异常值等,可有效帮助现场管理者对物料输送、料道规划、工位和物料区进行统一规划。同时可对比物流、工位设置方案与生产工艺的适配性,提前得知规划的生产物流方案是否存在浪费,可在方案实施时大幅降低试错成本,避免设备的过度投入,可将物料成本节约30%左右,最大化降低在传统工厂生产时发生的不确定性问题。
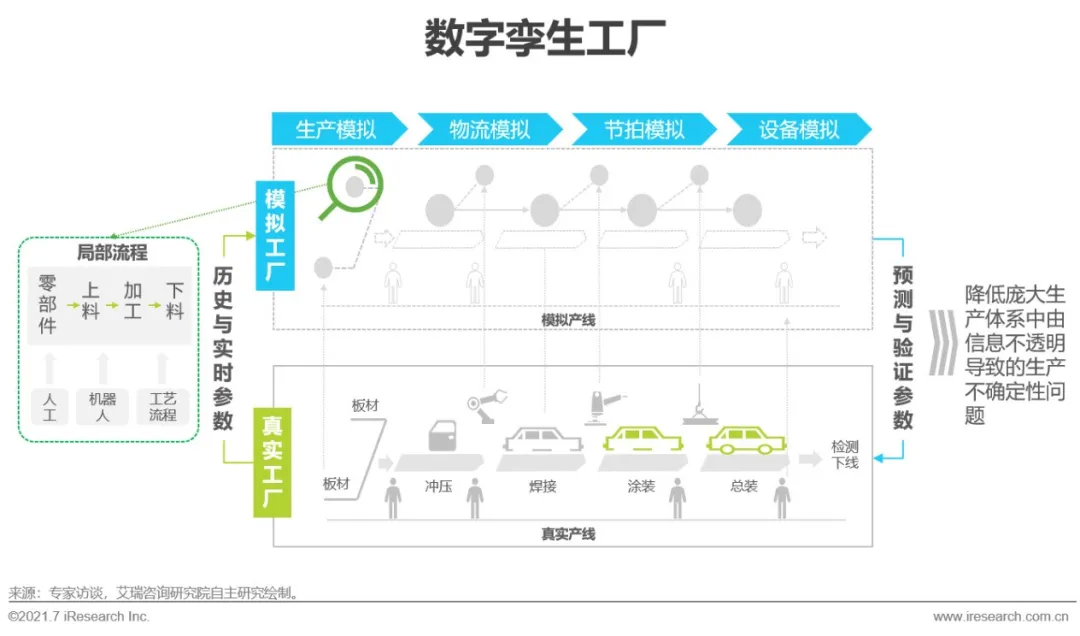
技术应用的终极目标—生产模式变革
柔性化模式令每下一辆汽车的生产都成为一个盲盒
任何新兴技术都并非为了应用而应用。在车企生产数字化进程中,技术应用的终极目标是利用数字工厂将传统汽车生产制造方式转变为柔性化生产方式,以便快速响应消费者个性化需求,以及降低为了满足消费者需求而产生的一切不确定性和风险,为下一阶段的智能化打下良好的基础。具体体现包含在冲压车间中以极短的时间内更换胎膜;在焊装车间中以机器人自主识别焊点位置和工艺要求;在涂装车间内自主完成油漆罐清洗同时降低资源浪费;在总装车间内AVG自动识别所需物料并及时配送。总之,在车企数字化转型过程中,前沿技术应用的目标并非在技术升级,而在完成一次历史性的生产方式变革;而变革后的未来工厂将具有快速而经济地适应生产变化的能力,和适应由需求改变引起的不确定性能力。
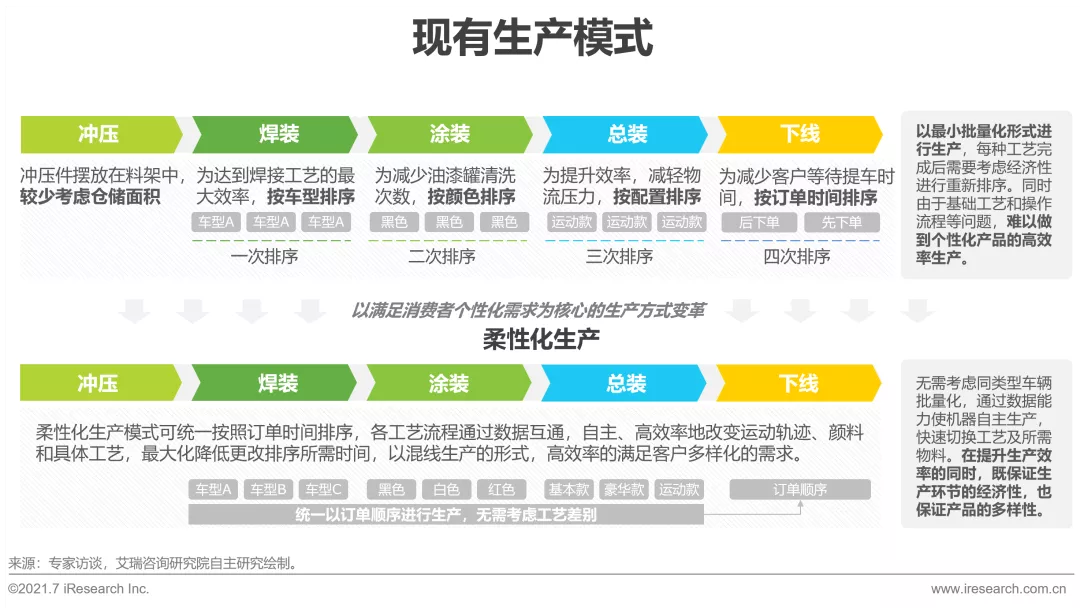
生产数字化转型的困境与挑战
缺乏顶层设计使企业数字化转型知易行难
生产各环节的数据、业务、流程、软件系统等打通都需要顶层构架的预先设计和规划,而缺乏了顶层设计便容易出现流程割裂、建设重复、标准不一的种种问题。更重要的是,在面临短期内的大量资金需求、部门间利益平衡和原有考核压力的问题时,缺乏顶层设计导致各部门间数字化目标难以对齐,担心JPH、资金等短期损失导致数字化内生动力不足,进而数字化进程受阻。尤其在部分国资背景车企,国资委和集团的考核集中在市占率、产销量和利润方面,除非承接国家研究课题拿到相应预算,否则使用先进科技的决策将极为谨慎。
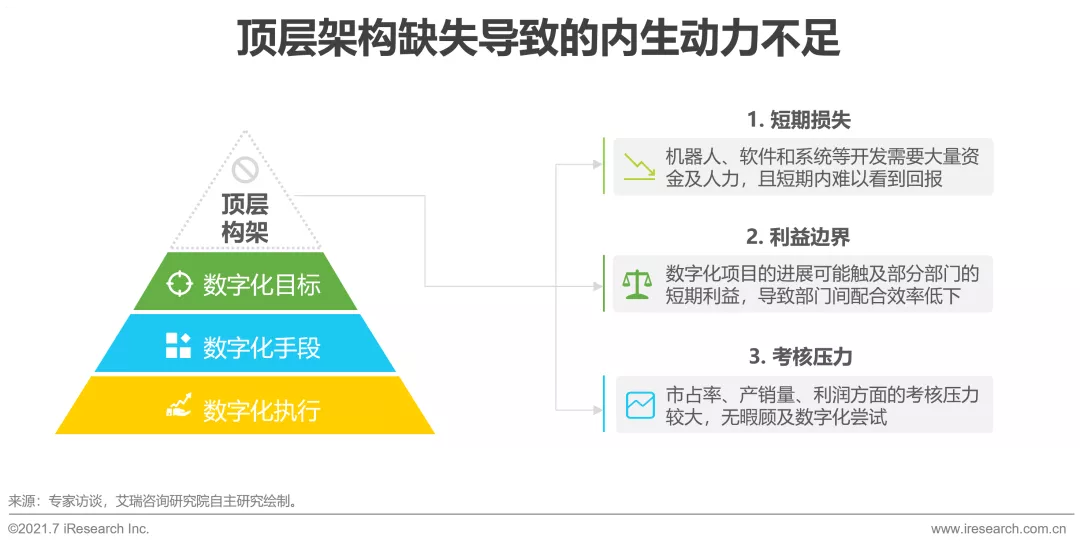
由于缺乏数字化认知导致的转型失灵
由于生产制造端的数字化转型仍然为新生事物,国内起步较晚,因此车企对此认知仍然处于参差不齐的阶段。在员工层面,IT人员认为数字化是软件和数据的利用;生产人员认为智能制造设备是数字化的体现,各部门如盲人摸象般的认知难以统一。在企业层面,部分管理者并未从其本质层面出发思考问题,认为数字化仅仅为了降本增效,忽略了其应对风险的本质,导致短期内难以达成降本增效的目标而在迷途中苦苦思索。同时,部分管理者容易将自动化和数字化混淆,更加导致了认知偏差。
生产数字化的本质体现在汽车产业业态、消费者需求和外部环境发生变化时第一时间应对风险和快速响应的能力;是在设备透明化,生产敏捷化的基础上以柔性生产的方式为客户定制个性化、小批量产品的能力;是帮助实现智能制造及工业4.0的必要手段和工具。而对此本质认知的偏差成为了数字化进程中的重要阻碍。
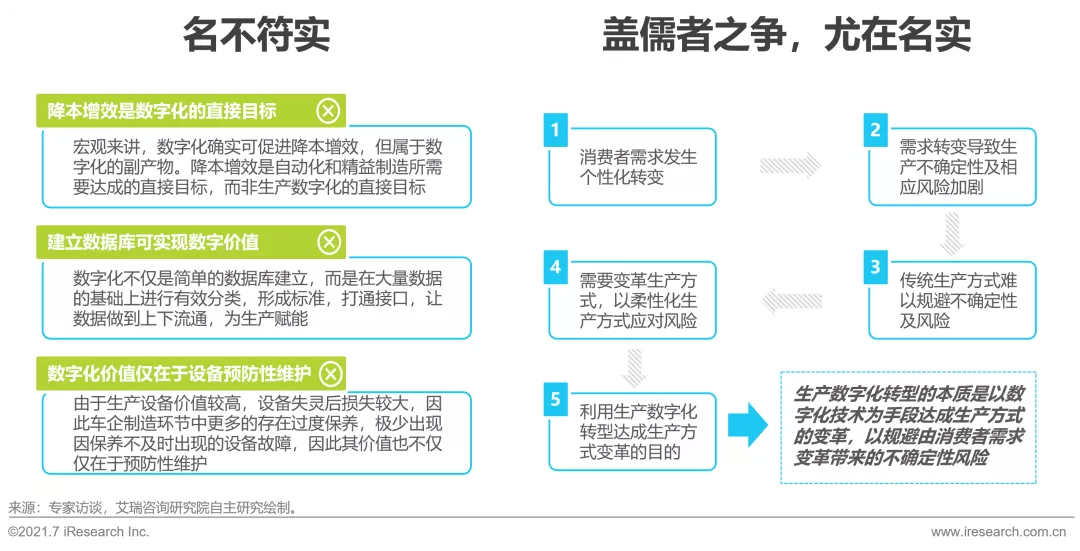
看重投资回报率,难以接受投资回报不明确下的巨额支出
由于数字化项目花费金额较大,同时车企为避免过度投资会谨慎考虑前期投资额并对投资报率极为重视,因此部分企业仅将数字化作为尝试性的前沿探索,不当做重要战略方向。更重要的是,由于在数字化前期难以快速见到回报且过程中存在诸多瓶颈,管理者为企业短中期利益考虑难以接受投资回报不明确情况下的巨额投资。虽然管理者此番考虑实属合理,但会一定程度上拖慢数字化转型的节奏甚至导致项目的半途而废,从而失去长期的市场竞争力。
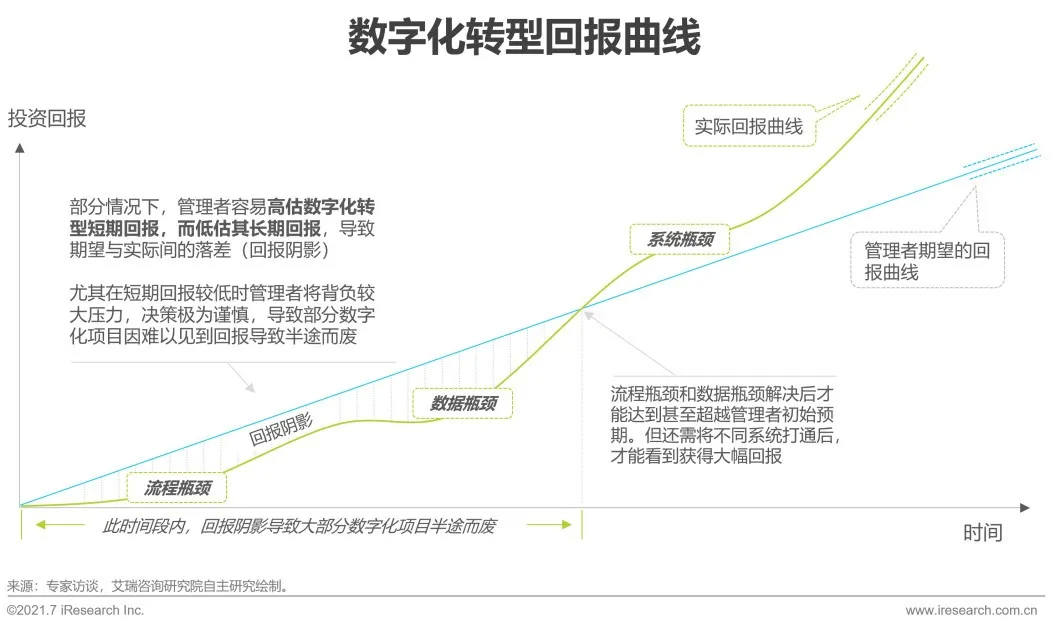
生产制造或是汽车生命周期中最难以受到重视的环节
汽车工业被称作“工业中的工业”,其产业链相对其他产业更长、更复杂;同时汽车的制造能力与其供应链、营销、品牌、口碑等有着极其密切的关系,因此汽车工业的微笑曲线理应更加平缓,而生产制造环节的价值理应更高,然而在整体汽车生命周期当中生产制造仍然是最不被集团高层重视的环节。虽然部分学者表示目前已经打破了传统的微笑曲线由中部向两端攀升的固定思维,但不得不承认的是生产制造的附加值仍然难以提升,因此生产制造在整体汽车价值链中处与较为尴尬的境地。由于销售量、利润、市占率等“硬指标”的压力,车企更加重视设计、研发和营销环节。数字化设计/研发可以加速汽车的更新迭代,数字化营销可以精准触达用户以完成销售指标,而对于生产制造环节的要求则为按照规定的质量及时间顺利交付即可。因此,当“硬指标”难以达成时,生产制造方面的数字化投入则变成了部分企业的负担和累赘。
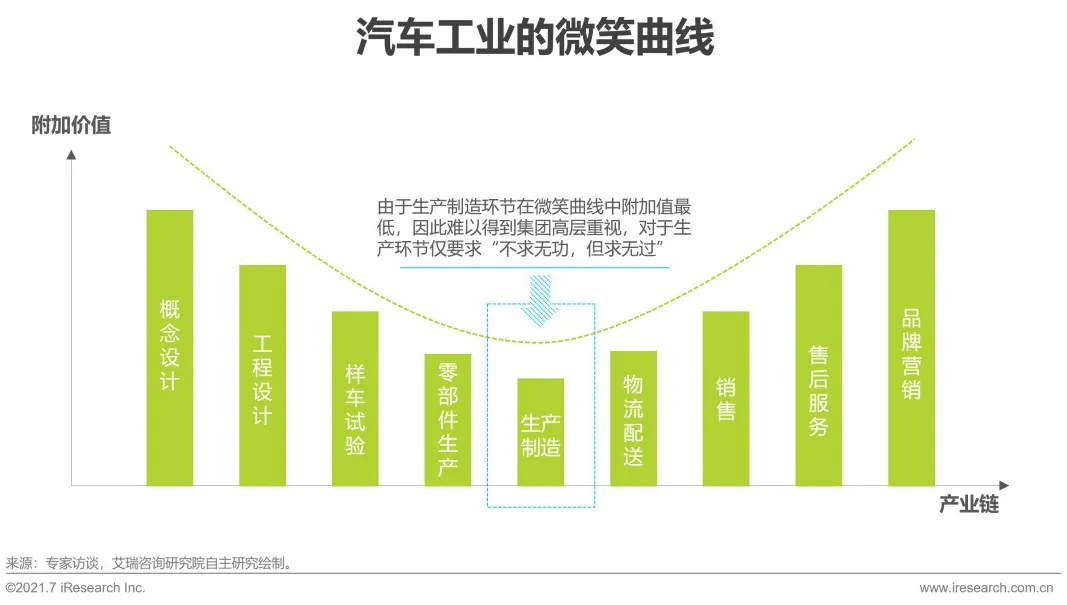
生产数字化转型关键成功因素
决策层的支持成为生产数字化转型成功的最关键的因素
自下而上和自上而下的推动数字化转型的差异极其明显。例如,在缺乏高层支持的情况下,虽各部门均可部署数字化技术但短期成本较高,如涂装车间改造多则需要二到三百台机器人,每台价格在几十万到几百万之间,在部门间配合和资金审批等事项中将会产生极大阻碍。同时,部门间在尚未建立数字化共识时,研发、生产、供应链等部门独立数字化难以产生实际意义甚至会出现反作用,例如通过工艺流程改造提高生产节拍后,供应链部门若无法做到数字化系统协同则会出现暂时的物料紧张问题。因此,数字化仅仅是转型工具,而通过部门间协同达成生产模式变革才是目的。而达到此目的则需要高层挂帅,自上而下的进行数字化进程,通过工艺、软件、系统等顶层架构减少各部门对数字化理解的偏差,建立科学的决策机制和流程机制,最大程度上减少数字化进程中所走的弯路。
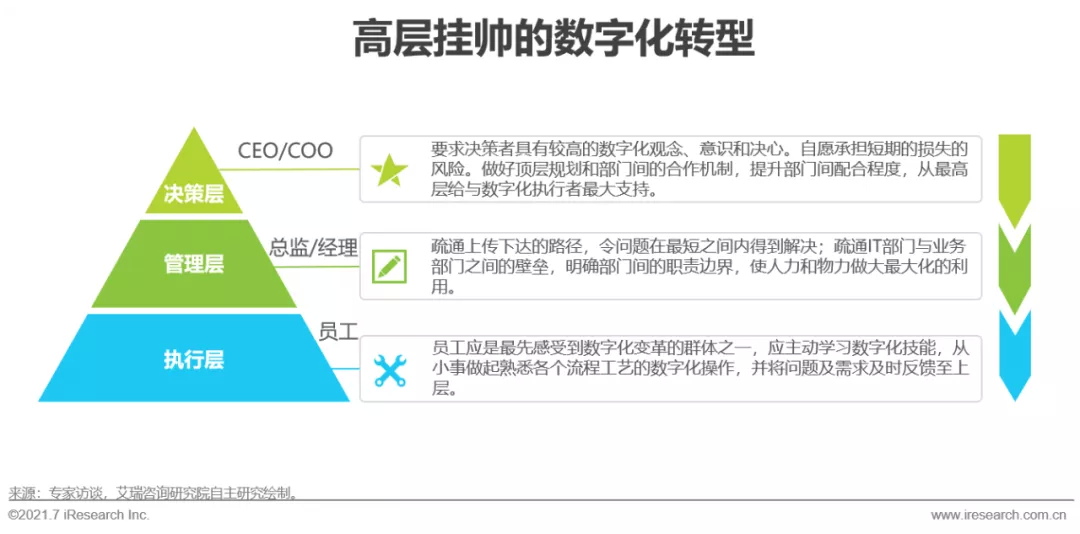
IT与生产双管齐下、有机融合是数字化转型落地的根本原则
通常IT部门与生产部门存在着不同的业务语言和对数字化的理解,因此在理解出现偏差时,生产人员认为技术人员缺乏技术能力,而技术人员则认为生产人员需求不合理,容易导致责任推诿及内部管理混乱,因此两者之间沟通机制的建立成为基础。同时,传统车企中IT等部门仅扮演边缘角色,而生产、业务部门由于直接与产销挂钩故话语权较大;当数字化来临后,由于数字化项目通常较为复杂,耗费资金较大,且由于其专业性导致生产及业务部门难以承担,因此IT部门被给予了较大权利与责任。此举引发两种问题,其一间接削弱了生产及业务部门的话语权,导致部门间利益博弈,配合意愿降低;其二IT部门在过多的被公司寄以厚望的同时,考核指标并未发生根本变化,导致内生动力不足。因此,IT部门和生产、业务部门需协同配合,双管齐下,在各自的职责范围中提高期望与产出之间的一致性。
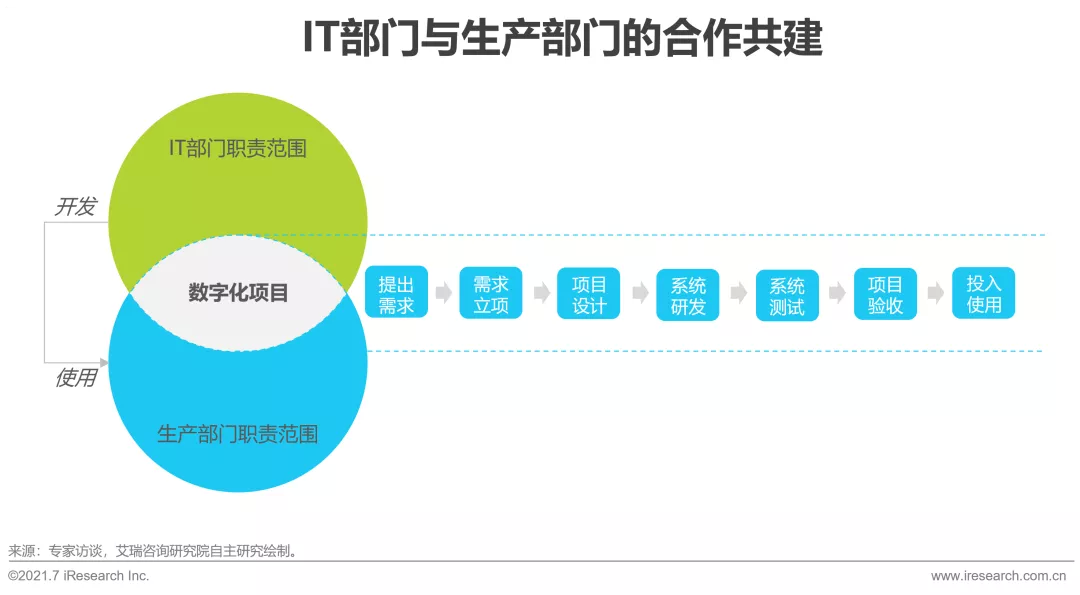
将梳理流程、统一数据作为数字化转型的源头
问渠那得清如许,为有源头活水来。在开始数字化项目之前企业生产环节的流程梳理十分关键,若线下流程混乱则线上流程将毫无意义,因此流程清晰后再做系统和软件的开发将事半功倍。生产、质控、物流等需求必须要从生产车间各个部门找到对应的生产负责人和工程师将流程厘清,明确流程机制的核心和业务流中的权责机制,否则软件开发完成后流程不同便不得不做系统的二次更改,造成人力、物力及财力的浪费。同时,每种物料、车型等在不同环节的编号、规格数据也需要在开发软件之间进行统一,规避不同格式、人称和操作手法导致的数据不统一的问题,为后期的数据分析及数据库打下基础。而对于供应商来讲更需要做到与车企的数据同步,提供统一标准的数据标签,尽可能达到零部件状态可追溯。
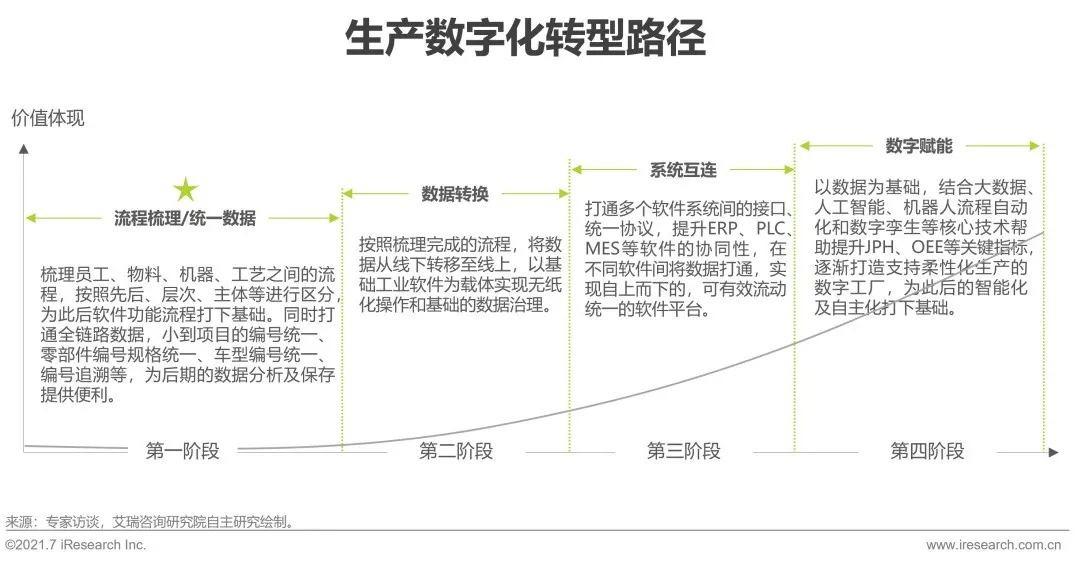
企业战略层:自上而下
在集团层面设立数字化部门,自上而下贯彻数字化路线
目前部分车企并未有专门的数字化部门负责相关项目,而以项目组或某一部门冠名的形式居多,其专业性仍有待考量。因此在数字化决策初期,企业应在集团层面建立数字化部门,任命生产与IT的复合型人才作为CDO,保证其与生产、业务部门的顺畅沟通。同时决策层在建立数字化转型路线后,需从长远考虑,从顶层设计出发向下贯彻,因为一旦总体系统模型建好后将来业务或者需求需要拓展,流程的兼容性以及不同供应商之间的系统兼容性可能对系统性能产生重大影响。同时,市场、消费者、技术、竞对等在不断变化,不应将数字化孤立的看待为静态的路线,相反应建立循环式流程,周期性的对上述各项因素进行判断,而认知的不断刷新也将促使企业走向适合自身的数字化道路。
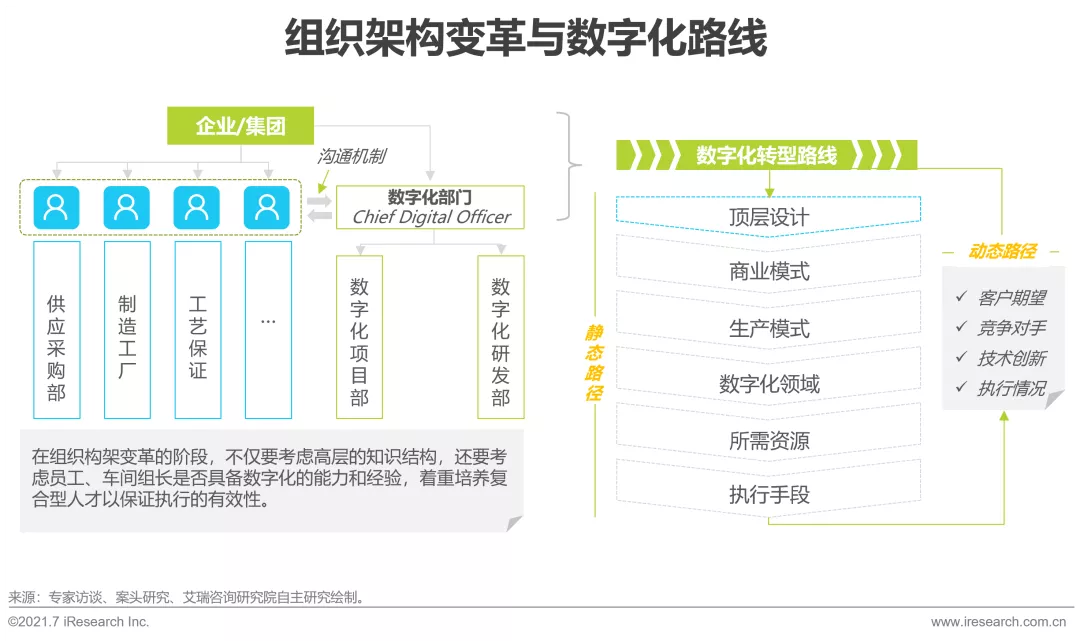
企业管理层:纲举目张
抓住自身企业数字化的关键所在,以点带面、小步快跑
车企每日被无数的伪数字化所包围,不排除部分软件企业以推销为目的将自身产品及服务包装为数字化概念,其动机仍有待商榷。而数字化并非是可以解决一切企业问题的良药,因此企业需要明确阶段性数字化目标和自身变革的细节,对应顶层设计和企业现状筛选出可以解决关键问题的数字化手段,只有对业务有实质性的提升,企业战略层才能看到价值从而给与资源支持。同时尝试从关键的小问题着手,做好数据标准和底层软件为将来的全面数字化和智能化打下基础,采取纲举目张、以点带面,小步快跑的方式进行数字化转型。此举可以将一次性的大额投资进行分摊,减轻短期内资金压力,降低对投资回报的担忧,进而有目的、有重点的促进生产环节的数字化转型。
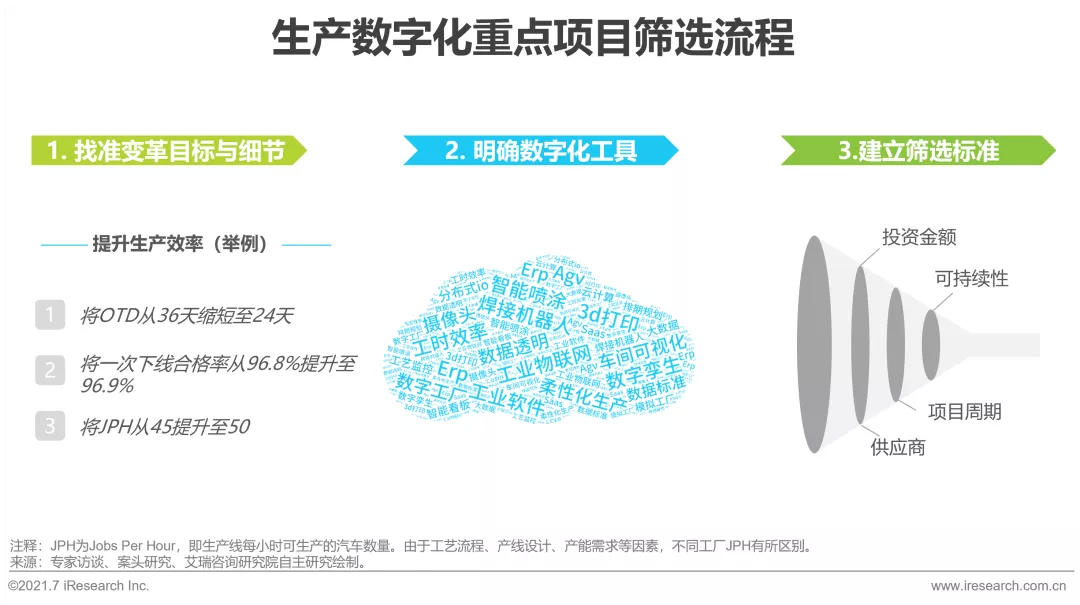
企业执行层:循序渐进
生产效率提升并非一蹴而就,配置临时人员可促进产能提升
生产效率的提升是车企数字化中关注较多的课题之一,而由于停线频率、物流问题、人员操作等不确定性因素,使用数字化工具得出的提升指标仍需经过现场验证和磨合才能真正体现价值。因此,工厂可采取配备候选人、提前测试等循序渐进的方式完成生产效率的提升。
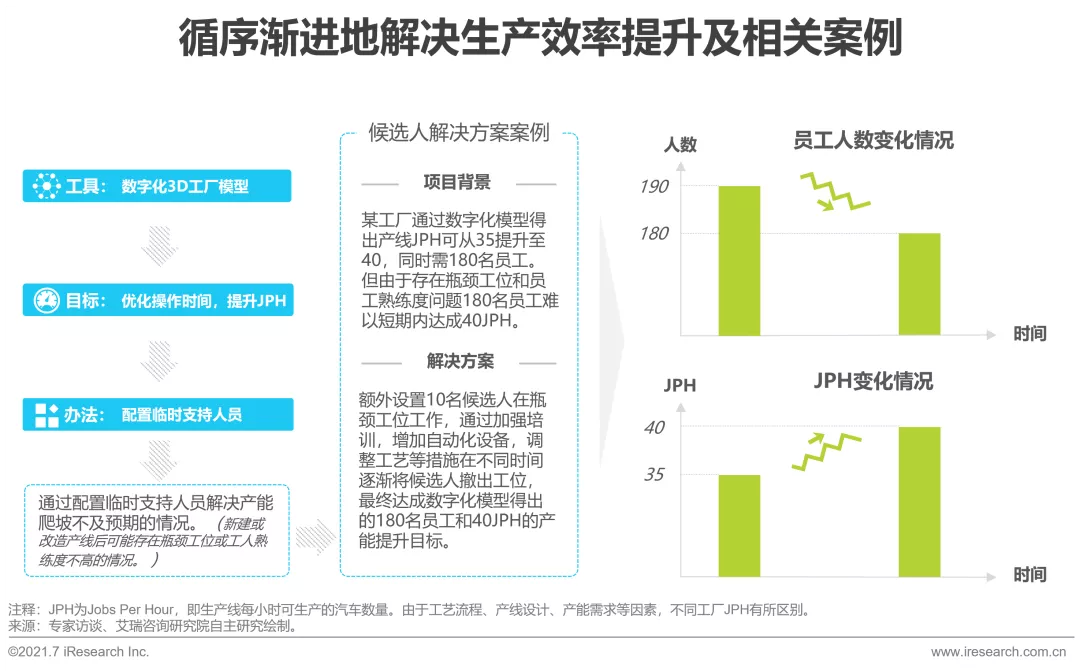
车企生产数字化水平评估模型
了解自身才能在竞争中胸有成竹
艾瑞针对生产数字化建立了评估模型,旨在帮助车企初步了解自身的数字化程度以便对自身竞争力做出基本判断。此模型结合了大量外部资料审阅与行业专家深度验证,包含24项评估指标并对其重要性进行分析和量化,内容涵盖软硬件、机器人、仿真模拟、标准化、生产模式等方面。
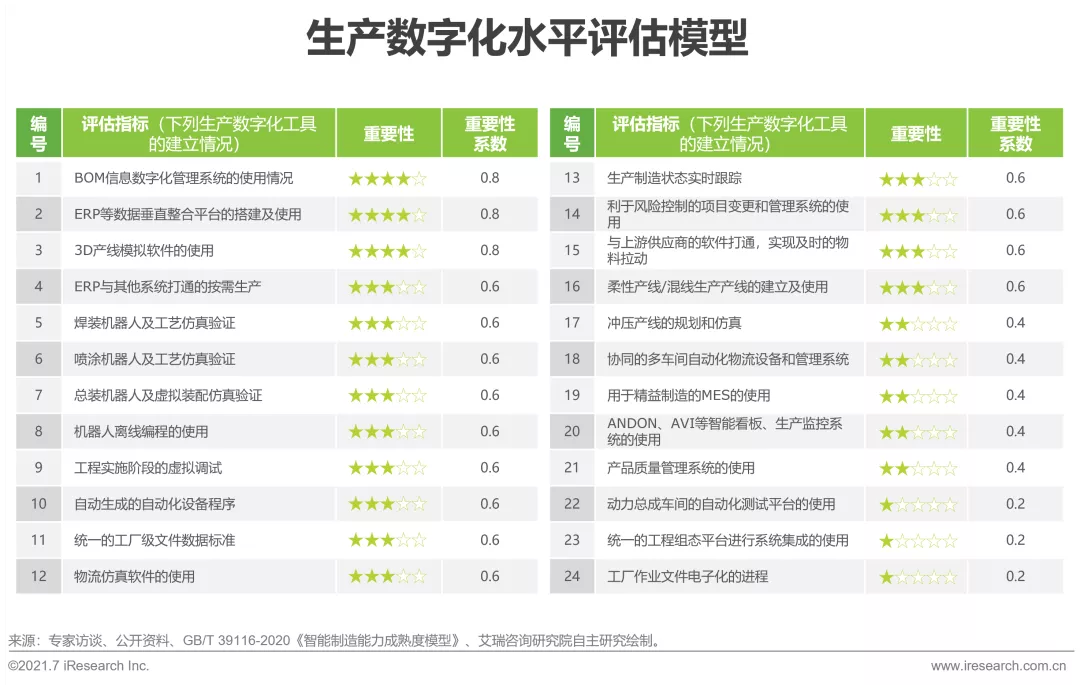
如何使用数字化模型进行自测?
合资车企表现更胜一筹,自主车企压力下精进不止
由于国内合资企业可以更有效的借鉴国外先进的制造经验,生产数字化水平较高。而自主车企虽然起步较晚,暂时稍显落后,但其拥抱数字化的态度与积极性不断提升,逐渐缩短与合资企业的差距。而新势力车企则后发优势明显,部分新势力工厂数字化程度极高,部分生产环节如冲压、焊接可达到95%以上甚至100%的自动化率,并利用数字化技术进行管理调度。
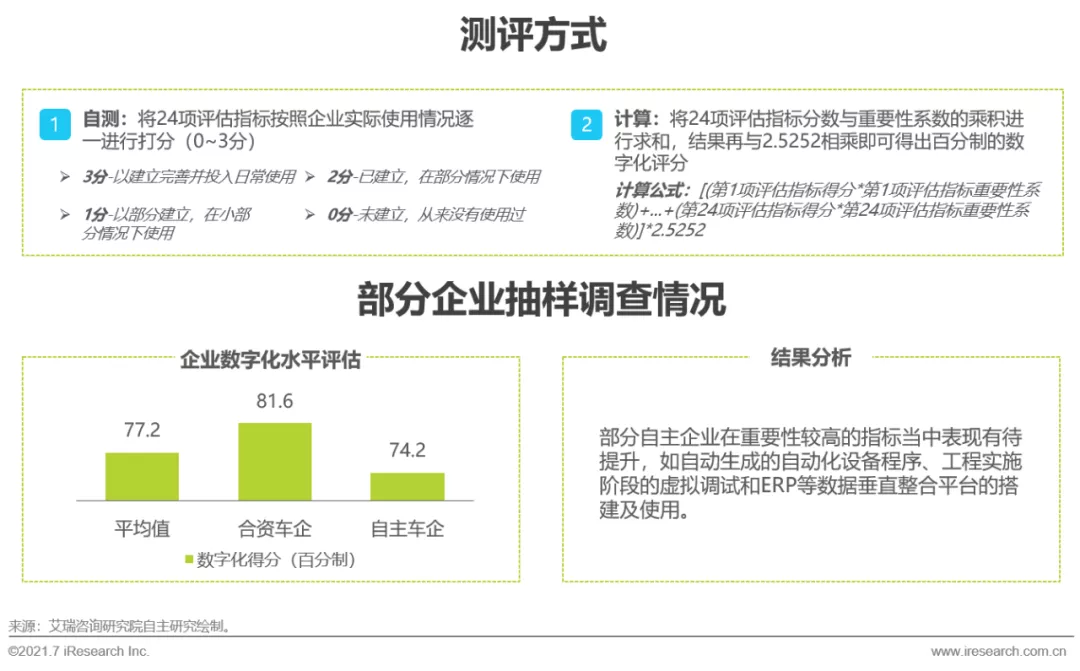
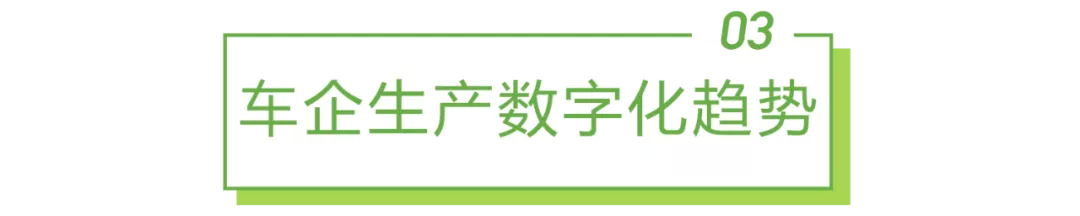
数据分析工具和人才需求不断增长
汽车产业数据量的增长将导致相关人才的巨大缺口
随着数字化趋势不断扩张,全球数据数据量将持续指数型增长,2020年数据量相当于世界上所有沙子的57倍,而多数为非结构化数据。在数字化工厂中,传感器、机器人等数据的处理及分析将成为汽车制造领域中的一大挑战,因此数据分析相关人才的重要性不言而喻,BI、Business Objects和Cognos等数据分析系统的使用将成为日常,而既了解汽车制造又能够熟练使用数据分析工具的人才将在行业中获得巨大的竞争力。
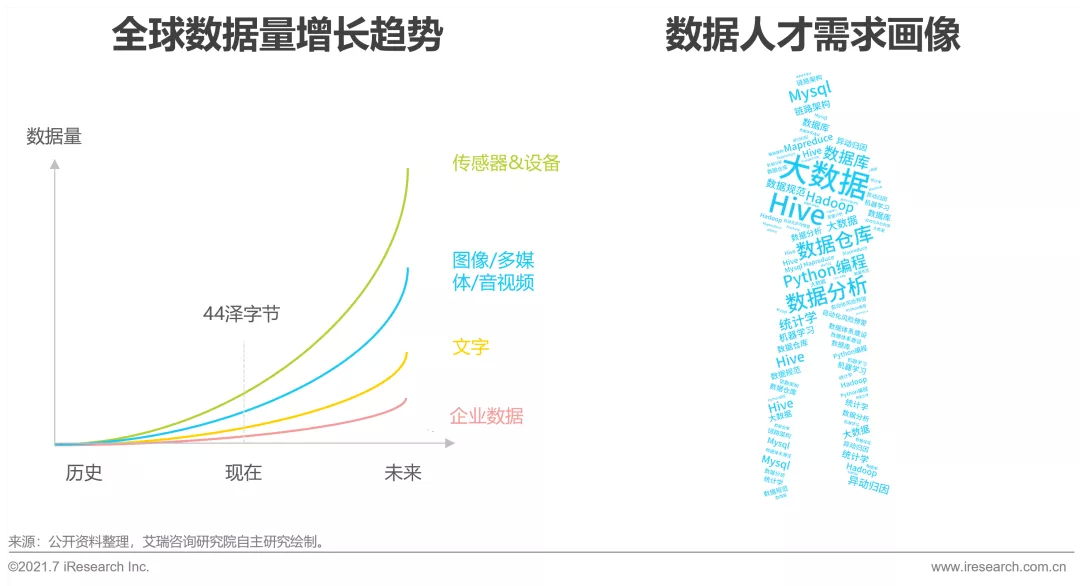
机器人在制造业中的持续优化及演进
人机共融的生产方式将重塑人们对制造业的刻板印象
2014年丁汉院士、杨学军和郑南宁院士主导推动了国家自然科学基金委重大研究计划“共融机器人基础理论与关键技术研究”,推动人、机、环境共融机器人的研究,包含了刚-柔-软耦合顺柔结构设计与动力学、多模态环境感知和人机互协作等方向,逐渐成为当前机器人的发展趋势。而协作机器人在汽车生产制造中的应用仍然取决于场景的开发,预计5~10年后将逐渐开始成熟。协作机器人的研究并非为了不断增加机器人的用量以取代人类,人类的智慧更不会因协作机器人的出现而停滞不前甚至衰退,而是在生产制造中相互适应、彼此支持的共同优化与演进。
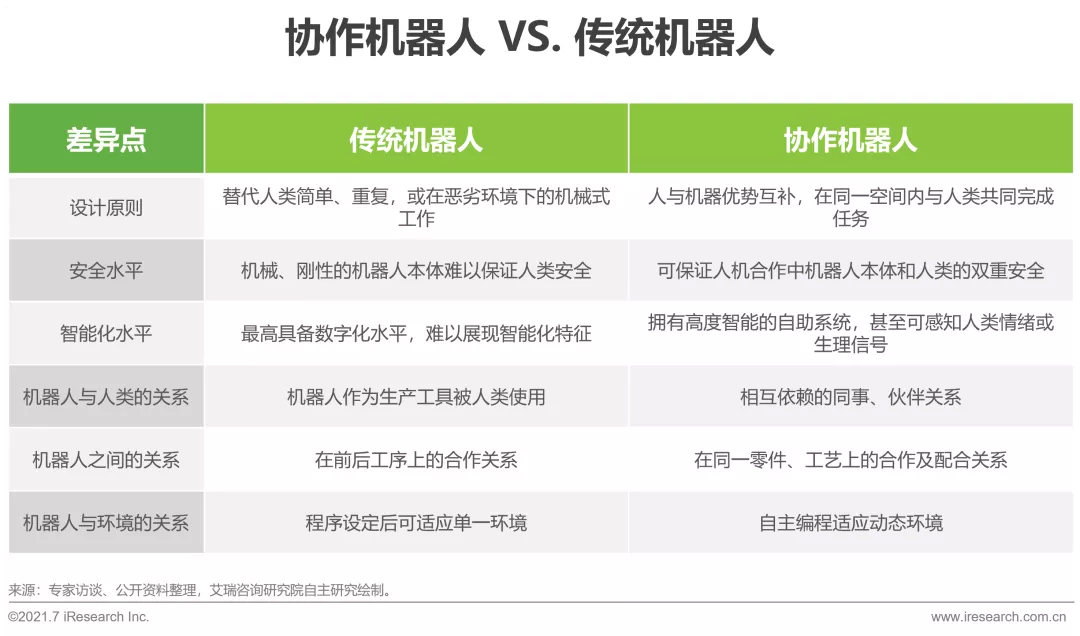
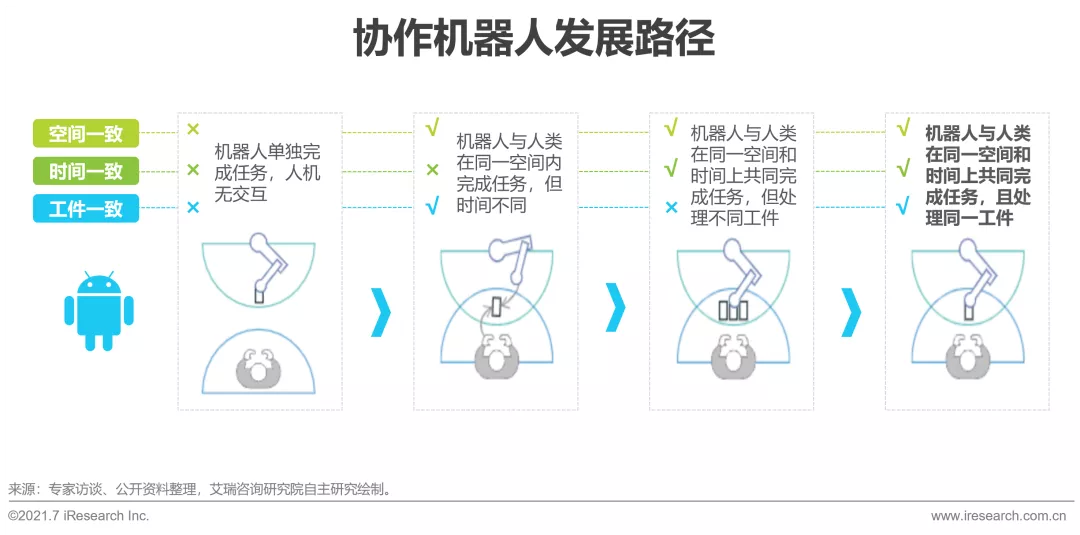
数字化服务商的不断成熟与发展
为解决车企实际痛点,服务商的产品价值将不断提升
除机器人或硬件服务商外,多数数字化服务商为互联网及IT企业,其互联网思维与传统的工业制造思维有所差异,而数字化也并非是简单的互联网与制造业的结合,因此部分车企在与数字化服务商合作后发现其实际产生的价值不如预期。而数字化服务商也在探索中不断成长,更加聚焦于解决车企的实际问题而被车企广泛认可,以BATH为代表的大型互联网企业正在不断夺取外商市场份额,而少部分宣传伪数字化概念的服务商将逐渐退出历史舞台。
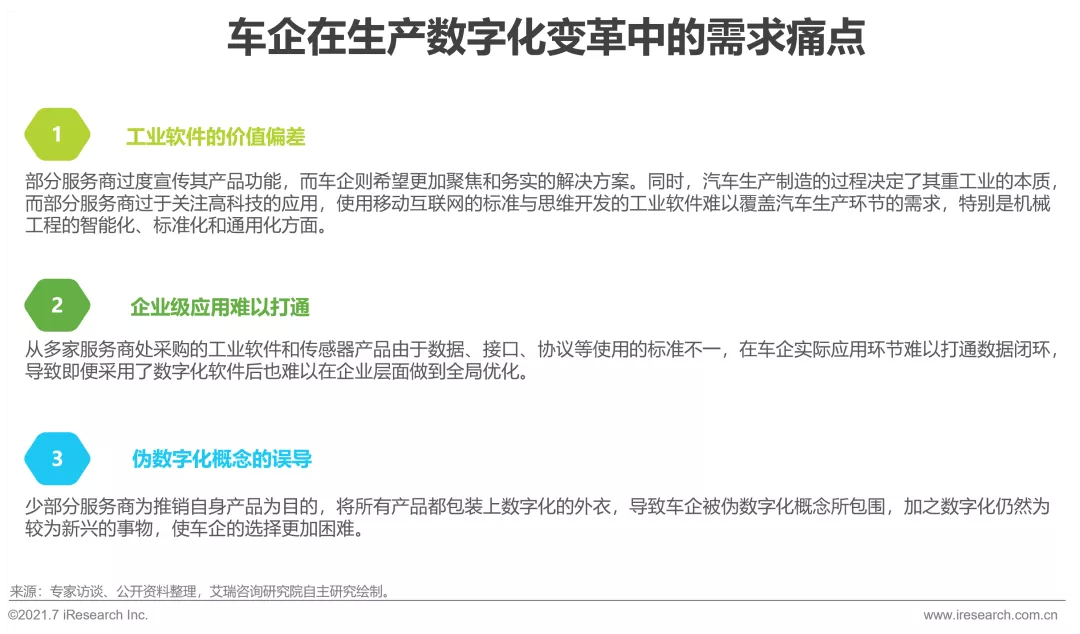
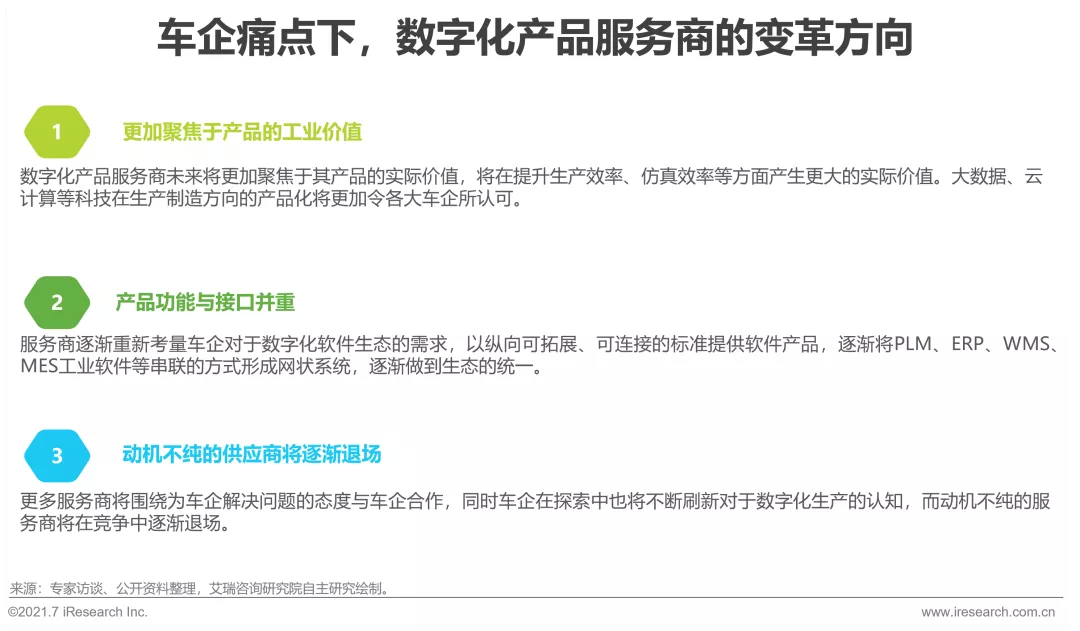
本文编选自“艾瑞咨询”,智通财经编辑:韩永昌。