本文来自微信公众号“乐睛智库精选”。
国内氢燃料电池产业:具备产业基础,整装待发
核心观点:氢燃料电池的底层技术决定了它是高能量密度、高能量转换率、环保无污染的能量来源,是理想汽车动力来源。目前国产氢燃料电池零部件、电堆已基本具备产业基础,重要系统配件主要依赖进口,正待政策春风起,以扬帆远航。
1、氢燃料电池工作原理决定了其是理想的汽车动力来源氢燃料电池与蓄电池电极反应物质贮存于电池内部不同,与内燃机相似,是将源源不断输入的燃料中的化学能转换为电能。
电池的负极供给燃料(氢气),正极供给氧化剂(氧气、空气),氢在负极上的催化剂的作用下失去电子,成为氢离子,进入电解液中,而电子则沿外部电路移向正极,在正极催化剂作用下与氧气结合生成水。
燃料电池技术原理与蓄电池、内燃机有差别,因而兼具两者的“燃料属性”、“环保属性”和“能量属性”,适应于重载、长里程、寒冷的运输场景。
目前我国在PEMFC燃料电池电堆及核心零部件的技术水平、成本控制水平均距离国外有差距,系统重要配件几乎依赖进口。
1、核心零部件、单体电池及电堆:我国能生产,但水平有差距我国具备核心零部件的产业基础,但距离国外高端水平有差距。目前催化剂的差距正在缩小,质子交换膜、碳纸、膜电极、双极板等差距还较大,是下一步技术攻关的发力点。
在电堆方面,目前国内最新的技术指标与国外差距小,但尚待验证。由于卡补贴现象严重,目前已装车电池功率、功率密度、工况寿命等核心指标距离国外水平有差距。最新技术水平至少需要经过2-3年的验证,才能确定稳定性方面与国外的差距。
2、重要系统配件几乎依赖进口重要系统配件几乎依赖进口,是技术攻关的核心领域。目前,在氢燃料电池的发动机里,燃料电池电堆的成本占比由50%左右上升至60%-70%,重要系统配件由50%左右下降至约30%。主要变动原因为氢气循环泵和储氢瓶成本的大幅下降。
将氢燃料电池的制造分为四步:第一步,制造膜电极;第二步,制造双极板;第三步,将膜电极和双极板连接在一起;第四步,检测制造好的电池的性能及安全性。
围绕这三个生产工序,有十类生产设备:高速搅拌机、催化剂喷涂机、干燥机、压合机、双极板涂层镀膜设备、切割设备、膜电极及电堆密封的点胶机、电堆检测设备、焊接机。
以动力锂电池产业化为鉴:以政策驱动为开端
核心观点:中央+地方层面积极出台政策,借鉴动力锂电产业化路径,我们判断投资时点上,目前的氢燃料电池对标2009年的动力锂电。
动力锂电由2009年“千城千辆”政策起步,经过10年的补贴实现产业化。燃料电池有望复制动力锂电的商业化路径。
自2009年起,动力锂电新能源汽车在十年的政策扶持下,逐渐实现了产业化,从2009年的全国产销约5000辆左右,逐步增长到2018年的生产127万辆、销售126万辆。
氢燃料电池的政策在4个方面可对标动力锂电:
(1)推广措施—均由中央+地方两级财政补贴为政策主要措施,早期关注先发优势,后期关注产品力优势。(2)推广领域—均为先商后乘,早期关注商用车领域,后期关注乘用车领域。(3)推广地域—均从部分城市重点投入到全国范围推广,早期关注车企的地域优势。(4)推广标准—国家标准、补贴标准会遵循越来越严格的路径,后期关注产品力优势。
不同之处在于配套设施方面,氢能源汽车是配套先行。动力锂电新能源汽车所需的充电站、换电站等配套设施起步晚,在2010-2011年仅是设立了标准,并没有鼓励政策,2014年起才逐渐加大了力度。
而氢燃料电池车所需的加氢站等配套设施在2018-2019年就有不少城市出台鼓励政策。
通过梳理我国动力锂电新能源汽车发展的脉络和现在产业链的状况,我们判断,目前氢能正处于产业导入期,时间点上可对标动力锂电的2009年,关键行业驱动力为财政补贴等产业扶持政策。
中央层面,2019年3月,氢能被首次写入政府工作报告,2019年10月国家能源委员会会议定下大力发展氢燃料电池的政策基调。
我们预计,财政部将于2019年Q4出台2020年后燃料电池的中央补贴标准。地方层面,2019年超过17个省份28个城市发布了氢能相关的地方政策,全国各地对氢能产业的规划布局正在提速。
目前我国的氢燃料电池政策投入最大的城市为浙江省(宁波市)、广东省(广州市、深圳市、佛山市)、江苏省(镇江市、张家港市)、上海市、重庆市。1、车载高压储氢是主流车辆的氢气来源有两条技术路线,一条是车载储氢技术路线,具体包括高压储氢、液氢储氢、金属氢化物储氢、浆液储氢四种技术实现方式;
另一条是随车制氢技术路线,具体包括汽油重整制氢装置、甲醇重整制氢装置、硼氢化钠水解制氢三种技术实现方式。
车载高压储氢是主流技术方式,即车内搭载储氢瓶作为能量储存装置。
国际上,从主要汽车厂商的燃料电池布局来看,车载纯氢储藏系统的车辆占据市场主导地位。
韩国现代途胜2013年2月,推出ix35,成为世界上第一辆量产版氢燃料电池汽车;日本丰田2014年12月,推出全全球第一款量产的Mirai氢燃料电池汽车,打开氢燃料电池商业化的大门;本田和奥迪分别宣布将在2016年推出其氢燃料电池汽车Clarity和Q6h-tron;福特、奔驰于2017年推出其氢燃料电池汽车Explorer和F-CELL;这些车型以高压储氢为主流搭载方式。
国内比较理想的方案也是采用高压储氢与储氢材料复合的储氢新模式,即在高压储氢器皿中填装质量较轻的储氢材料。
2、国内加氢站建设数量上或加速,单站规模上或增加车载高压储氢需要加氢站作为配套设施。
加氢站相当于燃油车的加油站,储氢瓶相当于国内以外供高压气氢站为主。
(1)根据氢气来源,加氢站可分为外供氢加氢站和内制氢加氢站。因氢气按照危化品管理,制氢站只能在化工园区内,故目前国内尚未有站内制氢加氢站。
外供氢加氢站内无制氢装置,氢气通过运氢车或者管道由制氢厂运输至加氢站,由压缩机压缩并输送入高压储氢瓶内存储,最终通过氢气加气机加注到燃料电池汽车中使用。
内制氢加氢站内建有制氢系统,氢气来源包括电解水制氢、天然气重整制氢等,制备好的氢气一般需经纯化、干燥后再进行压缩、存储及加注等步骤。
电解水制氢和天然气重整制氢技术由于设备便于安装、自动化程度较高,且天然气重整技术可依托天然气基础设施建设发展,因而在站内制氢加氢站中应用最多,欧洲内制氢加氢站主要采用这两种制氢方式。
(2)根据氢气存储方式的不同,可分为高压气氢站和液氢站。全球约30%的加氢站为液氢储运加氢站,主要分布在美国和日本,我国目前全部为高压气氢站,主要为35Mpa。
相比气氢储运,液氢储运加氢站占地面积更小,存储量更大,但是建设难度也相对更大,适合大规模加氢需求。高压氢气站按压力分,有35Mpa和70Mpa两种。70Mpa压缩密度高,等量氢气经70Mpa压缩后的体积比35Mpa小,但造价昂贵,运营费用高。
我国目前最便宜的制氢来源是煤炭重整制氢,工业副产氢来源充足,氢源不是限制燃料电池的因素。我们判断,在未来较长一段时间内,以煤炭重整制氢、工业副产氢源为主。
目前工业上制氢有三种较为成熟的技术路线:
(1)以煤炭、天然气等化石能源重整制氢。
以煤为原料制氢是目前成本最低的制氢方式,煤占制氢总成本的约50%,每小时产能为54万方合成器的装置在原料煤(600大卡,含碳量80%以上)价格600元/吨的情况下,制取氢气成本约8.85元/kg。以天然气为原料制氢是国外主流的制氢方式,天然气占制氢总成本的70%以上。
(2)以焦炉煤气、氯碱尾气、丙烷脱氢为代表的工业副产气制氢。
目前工业副产氢气的提纯成本在0.3-0.6元/公斤,考虑副产气体成本后,综合制氢成本约10-16元/公斤。
目前仅烧碱副产的氢气就足够1500+个日加氢规模为500kg的加氢站使用(截止2019H1,国内加氢站约25个左右),氢气来源充足。
我国是全球最大的焦炭生产国,每吨焦炭可产生焦炉煤气约350-450立方米,焦炉煤气中氢气含量约为54%-59%。
我国烧碱年产量基本稳定在3000万-3500万吨之间,副产氢气75-87.5万吨,其中约60%的氢气被配套聚氯乙烯和盐酸利用,剩余约28万-34万吨。
甲醇及合成氨工业、丙烷脱氢(PDH)项目的合成气含氢量在60%-95%之间。
我国甲醇产能8351万吨/年,甲醇驰放气有上百亿立方,其中氢气数十亿立方米。我国合成氨产能约1.5亿吨/年,每吨合成氨将产生150-250立方米的驰放气,可回收氢气约100万吨/年。截止2018年底,我国已建和在建的PDH项目17个,副产含氢约37万吨/年。
(3)电解水制氢。
目前电解水制氢技术主要有碱性水电解槽(AE)、质子交换膜水电解槽(PEM)和固体氧化物水电解槽(SOE),其中碱性水电解槽技术最为成熟,生产成本在电解水路线下最低,国内单台最大产气量为1000m3/h;质子交换膜电解槽流程简单,能效较高,国内单台最大产气量为50m3/h,但催化剂昂贵,成本高;固体氧化物水电解槽采用水蒸气电解,高温下工作,能效最高,但尚在实验室阶段。电解水法的主要成本在于电价,因其单位能耗较高(4-5千瓦时/立方氢气),一般认为当电价低于0.3元/千瓦时时,电解水法的成本接近煤炭或天然气重整制氢。
油氢混合站是未来加氢站发展的方向,目前中石油、中石化已经开始进行相关的研究和试验工作。
油氢混合站是指在现有的加油站、加气站的基础上,加入加氢功能设施,使站内具有加油、加气、加氢等多种功能,可以减少前期投入的成本、减少新增场地需求、缩短建设时间等问题。
根据《加氢站技术规范(国标GB50516-2010)》,加氢站可以单站建设,但需要重新选址、投入成本高,也可以与加油站、加气站一同建设,但需符合相关国家标准和规定。
中石油、中石化已经开始积极探索油氢混合站的可行性。2019年7月1日,国内首座油氢合建站——中国石化佛山樟坑油氢合建站正式建成,日供氢能力为500千克。
目前国内加氢站数量少,加氢规模不大,商业化加氢站稀缺,分布集中。截止2018年底,我国共运营23座加氢站,占全球的比例为6.23%。
加氢规模在500kg/日以上的有9座,占比39%;建站手续齐备的商业化加氢站6座,占比26%。
乘用车方面,国外商用的丰田Mira(i2014版)加满氢气需要5kg,单次续航在500公里左右;国内燃料客车配备的氢燃料电池加满氢气需要15kg-30kg之间,每公里需要消耗6-9kg氢气。
日加氢规模500kg的加氢站一天只能供应100辆乘用车,或30辆客车。我们预计,随着氢燃料电池车数量的增多,加氢站的数量会增加,同时单站加氢规模也会增加。
目前主要的拦路虎是加氢站前期建设成本高,其中设备成本约占70%。
根据《中国氢能源及燃料电池产业白皮书》的测算,国内建设一座日加氢能力500公斤、加注压力为35Mpa的加氢站至少需要1200万,相当于传统加油站的3倍。按中石化2019年4月向厚普股份采购的加氢设备合同来看,单套加氢站设备约1100万元。
主要设备为加氢机、储氢罐,目前设备的国产率不高,其中加氢机相当于加氢站的大脑,负责实现所有加注功能、压缩机的动作、储氢罐的开关。
加氢机的关键技术是控制氢气加注到气瓶过程中发热的程度,主要关注流速、剂量。
商业化运营的加氢站还需要考虑设备维护、运营、人工、税收等费用,折合加注成本在13-18元/公斤。但受规模效应(氢气加注量的增加)、油氢合建等建设方式、设备的国产化等影响,单位加注成本有下降的空间。
下游:客车、物流车领域有望优先受益
动力锂电汽车在客车、物流车领域一直做的不好,根本原因在于锂电池的能量密度比较低,且锂电池在低温环境下容量衰减很快(手机在北方的冬天掉电极快也是出于这个原因)。
在物流车这样的商用领域,下游客户以电商、快递、运输公司等市场化公司为主,重载、跨省跨市运营、夜间运营是常态,动力锂电池在这一部分的市场份额一直不高。
燃料电池汽车在动力方面可对标柴油车,所具备的的三个属性:燃料、能量、环保属性,它同时解决了内燃机燃油带来的的污染排放问题和电动汽车的里程焦虑和寿命问题,尤其适用于高负载、长距离、寒冷的运输场景中。在这些应用场景中,氢燃料电池具备先天的优势。
同时,结合我国动力锂电新能源汽车的发展轨迹看,对于一个处于产业引导初期的事物而言,降低成本走向商业化,取得消费者的价值认同,才是其拥有生命力的根本。
储氢站、燃料电池堆及成本是目前横亘在其产业化前面的三座大山。随着技术的迭代,目前的燃料电池系统和储氢站等高昂的成本问题,有望得以降低。
目前,我国已有少量客车、物流车进入商用阶段。自2017年起,一共有195辆车辆进入《新能源车推广目录》,其中客车占143款,运输车(物流车)43款,冷藏车+保温车共计占7款。
客车领域竞争较为激烈,北汽福田、佛山飞驰、金龙客车、上海申龙、宇通客车、中通客车均推出超过15款的客车;运输车、冷藏车、保温车领域,东风汽车、中通客车两家公司推出超过10款的运输车。
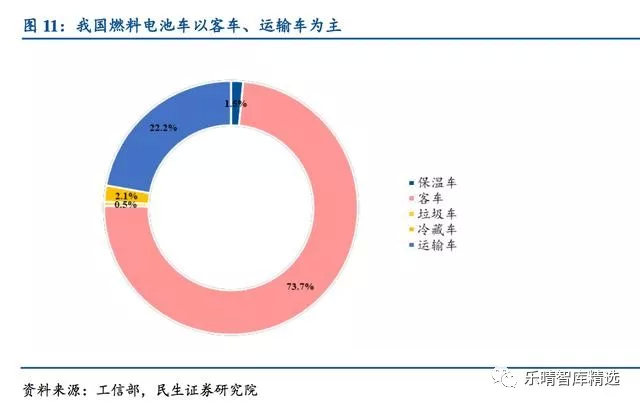
2018-2019年,我国燃料汽车的销售集中在商用车的客车领域,销量在千辆等级。根据中国汽车工业协会的数据,2018年,我国出售了1362辆燃料电池车,截止到2019年9月,当年出售了1228辆,均为客车、物流车,没有乘用车。
根据采购中标情况推算,目前氢燃料电池客车的单价在约150-300万左右,按1500辆年销量推算,目前燃料电池车市场规模在20-50亿元之间。
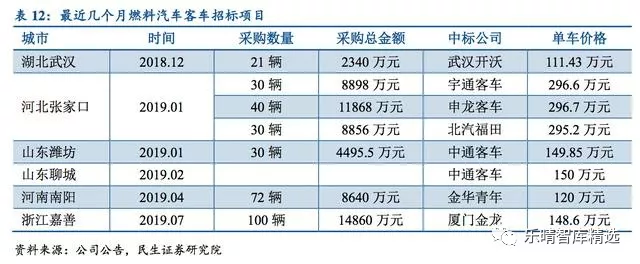
乘用车:国际上有量产经验,国内有尝试,需待技术积累成熟
需等待技术积累到一定的水平后,燃料电池才会逐步渗透到乘用车领域。理论上讲,乘用车的动力系统比商用车更难造,因为商用车动力系统可占据空间更大,对电池各项特征有比较高的容错性,售后方面也容易集中处理,乘用车则对各方面性能的要求都更高。
国际上有推出量产燃料电池乘用车的经验。国际车企已推出了几款成熟量产的燃料电池车,其中丰田于2014年推出的Mirai销量超过1万辆,且Mirai于2019年推出第二代产品。
韩国现代途胜2013年2月,推出ix35,成为世界上第一辆量产版氢燃料电池汽车;日本丰田2014年12月,推出全球第一款量产的Mirai氢燃料电池汽车,打开氢燃料电池商业化的大门;本田和奥迪分别宣布将在2016年推出其氢燃料电池汽车Clarity和Q6h-tron;福特、奔驰分别宣布将于2017年推出其氢燃料电池汽车Explorer和F-CELL,通用拟于2020年前推出雪佛兰EquinoX和凯迪拉克Provoq。
目前国内有少数厂家推出几款乘用车,但均未规模化生产或商用。2015年,上汽集团推出第四代采用荣威950车型平台的燃料电池车。我们预计,随着国内燃料电池技术的不断成熟、整车造价成本的降低、配套设施设备的完善,国内车企也将陆续推出燃料电池乘用车车型。